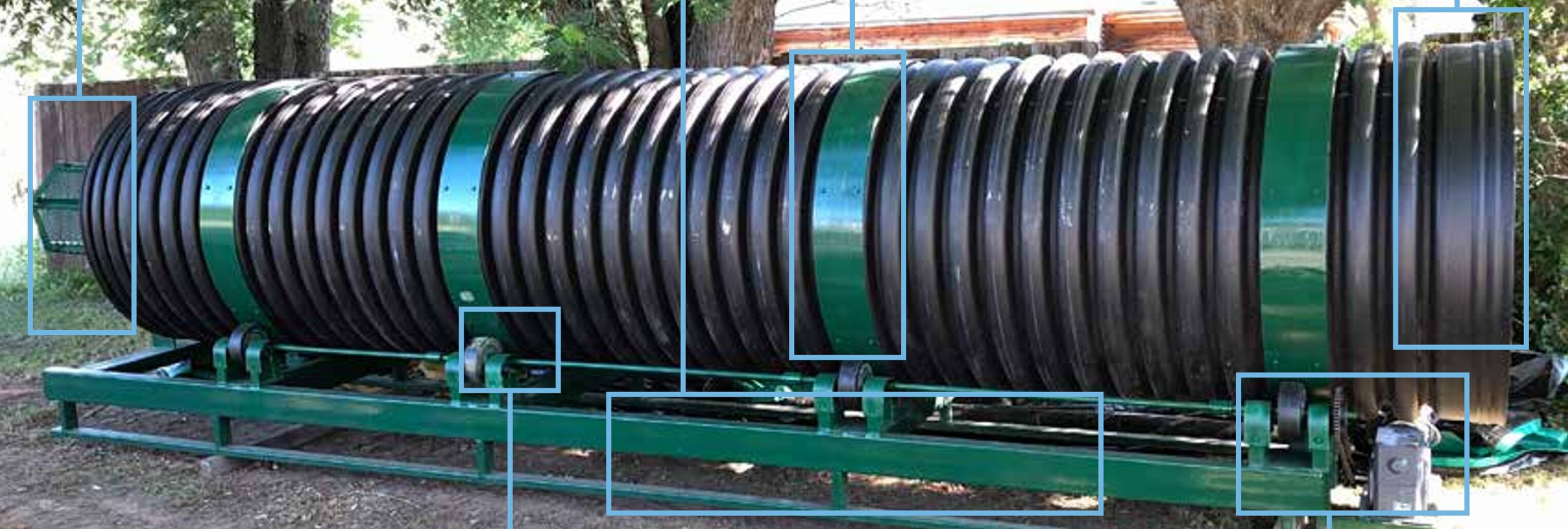
TorulaFeed™ from Corn and Wheat for Affordable and Healthy Protein
Most people agree that protein is good for you, carbs are bad for you and seed oils (omega-6 oils) are very bad for your health. Both corn and wheat contain about 10% protein, 70% carbs (starch) and 5% omega-6 oils. We’ve developed technologies to cost-effectively recover the protein from wheat and corn, convert the starch to yeast protein, and convert the omega-6 oils to yeast protein. TorulaFeed™ is a mixture of corn or wheat protein and Torula (Candida utilis) yeast.
The corn or wheat protein has a relatively mild flavor and the Torula yeast provides an intense umami (meaty) flavor, giving the mixture a meaty flavor which is very tasty to fish, animals and people.
Protein is more valuable when the constituent amino acids are a balanced source of food for fish, animals and people. Corn and wheat protein are deficient in lysine and rich in methionine amino acids while yeast protein is rich in lysine and deficient in methionine. A mixture of these two types of protein is therefore more balanced (and thus more valuable) than either of these two types of protein alone. This balance is the reason for the modern trend of vegan meals made from seitan (vital wheat gluten) mixed with nutritional yeast.
Our mission is to produce TorulaFeed that is less expensive and healthier than protein from legumes such as soybeans, peas and faba beans. These legumes contain many anti-nutritional factors (ANFs) that make them less than ideal for animal feed and human nutrition. These include trypsin inhibitors, lectins, oligosaccharides, phytic acid, saponins, antigens, isoflavones, tannins—all of which are harmful in feed. Carnivorous fish (salmonids/shrimp) suffer enteritis/growth issues at more than 30% soy. Young animals (piglets/chicks/calves) face digestive problems; poultry get diarrhea/reduced growth. TorulaFeed has no ANFs, yielding healthier fish/chicken/pigs and healthier plant-based protein for people.
The cost of producing yeast protein compared to soybean protein is one of the main reasons it hasn’t previously been used as a replacement for soybean protein, so we’ve focused on patented technologies to make low-cost production possible.
Our process reduces capital expenses (CAPEX) and operating expenses (OPEX) by using low-temperature enzymes to convert the starch in ground corn and wheat into simple sugars while simultaneously growing Torula yeast (Candida utilis) on these sugars in a rotating drum bioreactor (RDB). Air blown through the drum enables evaporative cooling, and we add water to maintain moisture without excess wetness. We harvest partial yeast batches, recycling the remainder along with enzymes to speed up subsequent cycles.
Over 50% of yeast production costs stem from raw materials. Using corn-derived sugars is our cheapest tested option, yielding not just single-cell protein (SCP) but also converting corn oil to protein and incorporating corn's protein, potassium and phosphorus into the feed. Wheat is a viable alternative, with its higher protein content (132 g/kg vs. corn's 94 g/kg) adding value.
This process is made possible by using our bacterial contamination control technique. This allows solid-state fermentation in an RDB with yeast/enzyme recycling and evaporative cooling—avoiding expensive submerged fermenters, heat exchangers, centrifuges, and dryers.
We focus on cost-effective SCP technologies for healthier feed than soy. We're licensing patents, tech, and designs to clients with cheap corn and wheat access and feed markets, targeting the USA, Brazil, Russia, India, China, Argentina, and Mexico.
Our core patent blocks bacterial growth by limiting nickel (less than 1 mg/kg) and using urea as the sole nitrogen source—yeast thrives without nickel, but bacteria cannot. Use of this patent enables evaporative cooling and yeast recycling.
We’ve produced some recipes using TorulaFeed to show how to use it to produce healthy and tasty hamburgers with a perfect balance of omega-6 and omega-3 fatty acids. TorulaFeed can also be used in other recipes for meatballs and ground beef. Food manufacturers can produce TorulaBurger™ patties for sale using similar recipes, preprepared for cooking.
Our portable design fits in 20-ft shipping containers, using corrugated High-Density Polyethylene (HDPE) rolling drums that are 2 m in diameter, and 5 m long. These drums are made from food-grade HDPE and don’t leach nickel like stainless steel does. These containers are factory-assembled, stackable (up to 4 high), transportable by truck/train, and support rapid large-scale setup.
TorulaFeed™ and TorulaBurger™ are trademarks of Hamrick Engineering.
Cost saving elements | Impact | Prerequisite |
---|---|---|
Solid-state fermentation with rolling drum | No centrifuge or spray dryer, low power, no foam, high oxygen transfer | |
Granular Starch Hydrolyzing Enzymes | No jet cooker or high temperatures | |
Simultaneous Saccharification and Fermentation | Faster production of yeast | |
Evaporative cooling | No plate heat exchanger or water chiller | Bacterial contamination control |
Corrugated HDPE rolling drum | 1/10 cost of stainless steel | Evaporative cooling |
Yeast recycling | Faster production of yeast | Bacterial contamination control |
Growing Torula yeast | Metabolizes the oil in corn and wheat to produce protein | |
Containerized | Mass production, easy install, stackable |
Contamination Control
Bacterial contamination is the top challenge in industrial-scale ethanol fermentation or yeast growth. Our patented method prevents it by using urea as the sole nitrogen source and keeping nickel below 1 mg/kg—eliminating acid washes or antibiotics. Urea is added gradually during simultaneous saccharification and fermentation (SSF), accelerating the process without issues. It works at pH 4-7.
PCT Patent WO2024092285A2
U.S. Patent No. 12,297,423
U.S. Patent App. No. 19/202,827, filed May 8, 2025
Rotating Drum Bioreactor
Our RDB fermenter leverages our contamination control patents for year-round aerobic yeast growth on hammer-milled corn and wheat. Its core is a corrugated HDPE rolling drum, enabling large, containerized, stackable units at less than $1,000/m³—vs. more than $15,000/m³ for traditional ones (e.g., corrugated HDPE rolling drum costs less than $1,000 vs. more than $9,000 for stainless steel). Operating costs are lower than submerged fermentation.
It uses granular starch hydrolyzing enzymes (GSHE: glucoamylase + alpha-amylase), SSF at 38°C with Torula yeast (aka Candida utilis and Cyberlindnera jadinii), and yeast/enzyme recycling for speed.
Evaporative cooling skips heat exchangers, cutting CAPEX/OPEX and cleaning needs. Drums self-clean via abrasion during rotation. Drying is cheap at ~50% moisture in the slurry. Units are containerized and automated.
Healthier than Soy Protein
Our RDB fermenter yields yeast that's healthier than soy protein and competitively priced. Soy farming relies on harmful herbicides/pesticides that enter the food chain, plus soy has anti-nutritional compounds (e.g., trypsin inhibitors, lectins). Yeast offers better amino acid balance, sustainability (less land needed), and nutrition for fish/chicken.
Our low CAPEX and OPEX make this nutritious alternative cost-effective.
Yeast from Corn and Wheat
Our RDB fermenter cost-effectively produces protein-rich yeast from ground corn and wheat. Starch is hydrolyzed to glucose using GSHE (no-cook) enzymes, with yeast grown simultaneously (SSF). This is the cheapest aerobic sugar source—mirroring POET's ethanol process but aerobic for yeast. Drying energy is low at ~50% moisture.
Torula yeast is Generally Recognized As Safe (GRAS), approved globally for consumption by fish, animals and people, is widely sold by Lallemand as a flavor enhancer, and has been safely used since the 1930s for fish, animal and human consumption.
We can boost the protein content of Torula yeast by metabolizing the oil in corn and wheat, thus reducing the omega-6 content of TorulaFeed.
TorulaFeed in Fish and Animal Feed and in Food
Composition of TorulaFeed
The protein-enriched dried mixture that we produce, TorulaFeed, has about 41% protein and is almost identical to a 55/45% mixture of Torula yeast and defatted Dried Distillers Grains with Solubles (DDGS) from corn ethanol plants. Both Torula yeast and DDGS are commonly used to replace soy in fish and animal feed, and the protein-rich mixture of the two is well suited to replace soy. Soy, pea and faba bean protein are also commonly used in foods as meat replacements, and TorulaFeed is a healthier alternative.
People require about 0.8 g of protein per day per kg of body weight. The average person weighs about 62 kg (137 lbs) and thus requires about 50 g of protein per day. If half of the daily protein requirements are supplied by TorulaFeed, this would require 25 g of protein from TorulaFeed - about 61 g of TorulaFeed per day, of which would be about 34 g of Candida utilis yeast per day. Under normal growth conditions, the RNA content of Candida utilis is about 10% of dry matter, so 34g of Candida utilis contains about 3.4 g RNA. The recommended maximum daily consumption of RNA is less than 2 g/day, so it’s necessary to reduce the RNA content of Candida utilis for human consumption. We reduce the phosphorus content of the fermentation broth to less than 10 mg P/liter in the last few hours of growth, which reduces the RNA content of Candida utilis to less than 5% of dry matter. This reduces the average daily consumption of RNA to below 2 g/day, and further reductions of phosphorus near the end of growth can further reduce this to well below 1 g/day.
High-temperature drying of TorulaFeed serves dual purposes: inactivating the yeast cells to render them non-viable and safe for consumption, while also enhancing digestibility by breaking down tough cell wall components. TorulaFeed has no lipids (fats) so high-temperature drying doesn’t produce any rancid flavors from the oil in corn and wheat. The lack of lipids In TorulaFeed also makes it possible to store TorulaFeed in dry form for long periods (fats can go rancid from oxygen). It is also enriched in B-vitamins. We produce both animal feed and hamburger patties with TorulaFeed by adding an 80/20% mixture of Canola oil and flaxseed oil to enrich TorulaFeed with equal amounts of omega-6 and omega-3 fatty acids.
Because Canola oil also contains tocopherol anti-oxidants (Vitamin E), the omega-3 fatty acids from flaxseed oil aren’t oxidized when this oil is used for frying or baking, making an ideal oil to incorporate in hamburger patties with a perfect balance of omega-6 and omega-3 fatty acids. This oil also tastes good. A 1:1 mixture of omega-6 and omega-3 fatty acids is also well suited for fish, chicken and pig feed nutrition.
Torula yeast has twice as much lysine as DDGS and DDGS has twice as much methionine as Torula yeast, so together they have a well-balanced amino acid composition. Modest amounts of lysine may need to be supplemented, depending on the type of feed. Both Torula yeast and DDGS are rich in glutamic acid, giving this mixture a platable, meaty taste, while still being suitable for vegetarians and vegans. This mixture is also enriched in all B-vitamins (except B-12).
DDGS isn’t well suited to adding to food because the high temperature in the ethanol beer well causes oxidation of the fatty acids in the DDGS, which makes food containing DDGS less palatable. Because our process converts the oil from corn and wheat to protein before using high-temperature drying, there’s little oxidation of the lipids in the corn/wheat solids, thus TorulaFeed tastes like corn meal or seitan with meat (but without the carbs and fats).
Health Aspects of TorulaFeed when consumed by Fish, Animals and People
TorulaFeed is healthy for fish, chicken, pigs, and people. Feed conversion ratios (kg feed/kg weight gain) are 1.0-2.0 for fish, 1.7-2.0 for chicken, 2.5-3.5 for pigs, and 6.0-10.0 for cattle (least efficient). Torula yeast's feed value dates to 1940s Germany. Global production: ~140M tons poultry, 110M tons pigs, 90M tons aquaculture yearly.
Key health aspects: essential amino acids and fatty acids.
Essential Amino Acids
These must come from diet (fish/chicken/pigs/people can't synthesize them). Nine essentials:
Histidine - Growth, tissue repair, histamine.
Isoleucine - Muscle metabolism, energy, hemoglobin.
Leucine - Muscle synthesis, repair.
Lysine - Protein synthesis, hormones, enzymes.
Methionine - Detox, metabolism, sulfur compounds.
Phenylalanine - Neurotransmitter precursor (tyrosine, dopamine, norepinephrine).
Threonine - Collagen, elastin, immunity.
Tryptophan - Serotonin/melatonin precursor (mood/sleep).
Valine - Muscle growth, energy, repair.
Arginine is also essential for fish/chicken/pigs. TorulaFeed provides a good balance of amino acids, plus biotin and B-vitamins (except B12).
Essential Fatty Acids
Peoples can't produce these fatty acids, and without them people can’t live::
Alpha-Linolenic Acid (ALA, omega-3): Heart/brain health, anti-inflammation (in flaxseeds, chia, walnuts).
Linoleic Acid (LA, omega-6): Skin/hair, growth, membranes (in vegetable oils, nuts).
There are metabolic disorders caused by consuming an excess of omega-6 fatty acids and TorulaFeed along with an 80/20% mixture of Canola oil and flaxseed oil produces a feed that has equal amounts of ALA and LA. The human body converts them to EPA/DHA and a balance of ALA and LA in the diet prevents inflammation caused by too much LA.
Soybeans, peas and faba beans have an omega-6 excess and no omega-3/EPA/DHA, leading to poor health when consumed by people, either directly or indirectly. Yeast is healthier to consume.
Anti-Nutritional Factors (ANFs) in Legumes
Legumes such as soybeans, peas, and faba beans, contain many anti-nutritional factors that make them less than ideal for feeding to fish, animals and people. These include trypsin inhibitors, lectins, oligosaccharides, phytic acid, saponins, antigens, isoflavones, tannins—all of which are harmful in feed. Carnivorous fish (salmonids/shrimp) suffer enteritis/growth issues at more than 30% soy. Young animals (piglets/chicks/calves) face digestive problems; poultry get diarrhea/reduced growth. Yeast has no ANFs, yielding healthier fish/chicken/pigs.
Enhancing Digestibility of TorulaFeed
There are no ANFs in yeast and grain residuals, but phytate and the non-starch polysaccharide (NSP) arabinoxylan can reduce the digestibility of TorulaFeed.
Grains contain phytate, which binds phosphate and causes chelation of many critical minerals. Even though Candida utilis secretes phytase to free the phosphate in phytate, some supplementation with phytase during growth of TorulaFeed may be helpful.
Arabinoxylan from grain is indigestible by fish, chickens, pigs and people. Even though Candida utilis secretes xylanase, some supplementation with xylanase during fermentation may increase the yield of Candida utilis (which grows on xylose and arabinose) and improve the digestibility of TorulaFeed.
Animal | Recommended Inclusion Level of TorulaFeed | Key Basis for Recommendation |
---|---|---|
Salmon | 20% (up to 25% in some trials) | No adverse growth or health effects; potential gut benefits; higher may disrupt microbiome in mixed diets. |
Chicken | 20% | Maintains performance and carcass yield; higher worsens feed efficiency. |
Pig | 20-26% | No negative growth or diarrhea; improves efficiency; up to 40% protein replacement. |
Dog | Up to 20% | High palatability and digestibility, anti-inflammatory benefits; no regulatory limit, but aligned with studies. |
Cat | 20% | High palatability and digestibility; limited by fecal quality concerns. |
Using TorulaFeed in Food
TorulaFeed is a dried mixture of the processed ground corn and wheat solids and Torula yeast that taste like meat. It doesn’t require refrigeration and can be rapidly reconstituted as a healthy hamburger meat (ground beef) replacement. It is well suited to any market with health-conscious, vegetarian and vegan consumers. It is tasty, with a nutty, smoky, or umami flavor profile derived from the yeast, combined with the milder, grain-like taste of the corn and wheat residues. Torula yeast is well-established as a flavor enhancer in foods, where it is valued for its savory qualities and ability to improve overall palatability in various products. It is suitable for inclusion in foods, because both ground grain and Torula yeast are recognized as safe for consumption (with Torula yeast holding GRAS status from the FDA), and because similar yeast-based single-cell protein products or fermented substrates are already incorporated into items like seasonings, spreads, soups, sauces, snacks, and vegetarian alternatives.
TorulaFeed has no dietary carbs, has a good balance of essential amino acids and is low-fat (no lipids), making for an especially healthy addition to our diet.
TorulaFeed is produced with reduced ribonucleic acid (RNA) content, which solves problems with elevated uric acid levels from high nucleic acid content. The process described uses food-grade enzymes and a yeast strain extensively utilized in the food industry, supporting its suitability.
Recipes Using TorulaFeed for Vegan Burgers
Common elements in all recipies
The oil is an 80/20% mixture of Canola oil and flaxseed oil, optionally supplemented with flavors such as truffle.
The binder is either E461 methylcellulose or ground flaxseed. If ground flaxseed, add an equal amount of Canola oil.
The addition of Canola oil makes a 1:1 ratio of omega-6 to omega-3 fatty acids, and adds antioxidants.
Basic Low-Carb Vegan Burger Recipe
This straightforward recipe emphasizes TorulaFeed flavor with a binder for a for a firm texture. It's minimally seasoned to highlight the umami from the Torula yeast, keeping net carbs low. Yields 4 patties (about 100g each after cooking).
Ingredients:
200g TorulaFeed
15g binder; absorbs moisture
5g mixed spices (e.g., onion powder, garlic powder, smoked paprika)
2g salt
150-180ml water (adjust for consistency)
10g oil (for mixing or cooking; adds minimal carbs)
Instructions:
Mix the TorulaFeed, binder, spices, and salt in a bowl.
Gradually incorporate water and oil, stirring until a cohesive dough forms (let sit 10-15 minutes to gel and bind).
Divide into 4 portions and shape into patties.
Pan-fry in a non-stick skillet over medium heat for 4-5 minutes per side until crispy or bake at 190°C (375°F) for 15-20 minutes.
Serve with low-carb toppings like sliced tomatoes or vegan cheese.
Nutritional Notes:
About 19.6g protein per patty
No net carbs per patty
About 1g omega-6 and 1g omega-3 fatty acids per patty
Spinach-Infused Low-Carb Vegan Burger Recipe
This variation adds finely chopped spinach for added moisture and nutrients, binder without eggs or grains. It maintains a low-carb count with a fresh, green flavor profile. Yields 4 patties.
Ingredients:
200g TorulaFeed
100g fresh spinach (chopped and wilted to reduce volume)
12g binder
5g herbs and spices (e.g., basil, cumin, black pepper)
2g salt
120ml water
8g oil (for wilting spinach and binding)
Instructions:
Wilt chopped spinach in 4g oil over medium heat for 2-3 minutes, then cool.
Combine TorulaFeed, binder, herbs, spices, and salt.
Mix in wilted spinach, water, and remaining oil; rest 10 minutes for binding.
Form 4 patties and grill or pan-fry for 5 minutes per side.
Enjoy on a bed of greens for an ultra-low-carb meal.
Eggplant and Spice Low-Carb Vegan Burger Recipe
Incorporating roasted eggplant for a smoky, meaty texture, this formula uses the binder to make a firm patty, resulting in ~8g net carbs per patty. The eggplant adds volume without significant protein or carbs. Yields 4 patties.
Ingredients:
200g TorulaFeed
80g eggplant (diced and roasted)
14g binder
6g spices (e.g., chili powder, coriander, turmeric)
2g salt
140ml water
10g oil (for roasting and mixing)
Instructions:
Dice eggplant, toss with 5g oil, and roast at 200°C (400°F) for 15 minutes until soft.
Mash roasted eggplant slightly and mix with TorulaFeed, binder, spices, and salt.
Add water and remaining oil; let mixture hydrate for 15 minutes.
Shape into 4 patties and bake at 190°C (375°F) for 20 minutes, flipping once, or pan-fry.
Pair with pickled veggies for added tang.
Using E461 Methylcellulose as a Binder
The market leaders in vegan meat patties are Impossible Burger, Beyond Burger, Gardein Ultimate Plant-Based Burger, Lightlife Plant-Based Burger, and Incogmeato Burger Patties. All use E461 methylcellulose as a binder in their plant-based burger patties, which produces a juicier, meat-like texture that some people prefer. This firms up when heated, helping patties hold shape during cooking and offering a juicy bite when cooled. Methylcellulose is derived from plant-based cellulose fiber, is approved for food use worldwide and is relatively inexpensive.
Using Flaxseed as a Binder
Ground flaxseed, when combined with equal amounts of Canola oil, also makes a healthy binder. It’s not quite as firm when cooking, but some consumers feel it’s more natural than methylcellulose, adds equal amounts of omega-6 and omega-3 fatty acids and is quite tasty. When combined with Canola oil’s antioxidants, it doesn’t produce off-flavors from peroxidation when frying.
Cost of Protein in Foods
When comparing the cost per kg of protein of different foods, commercially available vegan meat patties are 3 times more expensive than ground beef and almost 50 times more expensive than TorulaBurger™ (see below). Vegan meat patties are marketed to wealthy consumers who aren’t price-sensitive to the cost of food, while TorulaBurger is a low-cost source of protein as healthy as salmon, but at 1/30 the price per kg of protein in salmon.
Protein source | Retail cost per kg protein | Omega-6 : Omega-3 ratio |
---|---|---|
Impossible Burger Patty | $157/kg | 200 : 1 |
Beyond Burger Patty | $124/kg | 11 : 1 |
Salmon Fillet (Atlantic, farmed) | $85/kg | 0.7 : 1 |
Ground Beef (85-90% lean) | $51/kg | 20 : 1 (2 : 1 grass-fed) |
Eggs | $48/kg | 16 : 1 (4 : 1 free-range) |
Pork Loin (boneless, skin) | $31/kg | 34 : 1 |
Chicken Breast (boneless, skinless) | $30/kg | 26 : 1 |
TorulaBurger™ | $3/kg | 1 : 1 |
Economics of Producing Yeast Protein from Ground Corn
Over 50% of yeast costs come from substrates; corn-hydrolyzed sugars are cheapest. Viability relies on RDB's low costs, cheap inputs, and high-value SCP for feed.
CAPEX: RDB at less than $1,000/m³ (50-80% below traditional $15,000/m³) for modular plants.
OPEX:
Substrates: 35-62% of costs; at $150/MT corn, ~$390/MT SCP (0.385 MT SCP/MT corn, from 70% starch).
Other: Enzymes, urea, rotation/cooling energy, drying. Evaporative/self-cleaning skips maintenance ($0.05-0.10/kg SCP saved); 50% moisture drying cheaper than 90%. Non-substrate: $200-300/MT SCP.
Labor/Utilities: Minimal via automation; low energy in containers.
Yields/Revenue: ~385 kg SCP/MT substrate (45-50% protein). Fodder yeast + DDGS: $500-1,000/MT (vs. soy meal ~$400/MT). Protein basis: SCP $800-1,000/MT vs. soy $890/MT, with superior nutrition. Revenue: $600-800/MT.
Profitability: Substrate $390/MT SCP; total cost $600-700/MT; break-even $550-650/MT; ROI 20-30% (5-year, 50k MT/year plant); margins 20-40% in high-demand areas. Pilot needed for commercialization.
Rolling Drum Bioreactor Clean-in-Place (CIP)
When growing Candida utilis in a rolling drum bioreactor using the non-starch parts of corn and wheat (i.e. bran) for support, the particulate nature of moistened bran, combined with the drum's rotation at 3 rpm and the presence of 8 lifters (150 mm high), promotes constant tumbling and cascading of the substrate. This mechanical action generates abrasion between the bran particles and the drum walls, which are made of high-density polyethylene (HDPE)—a smooth, non-stick material with low surface energy that inherently resists adhesion.
Abrasion from the tumbling substrate effectively scours the drum interior, preventing the accumulation of material on the walls. Literature on RDBs for SSF (including with wheat bran) emphasizes challenges like heat transfer, mixing, and contamination but does not report wall fouling or biofilm thickening as issues, even in long-term operations.
Candida utilis primarily grows on the bran particles rather than forming extensive biofilms on the drum surfaces, especially under the dryish, aerated conditions with evaporative cooling and pneumatic conveying. The continuous addition and removal of bran further maintains dynamic flow, reducing opportunities for static buildup.
Thus, the abrasion of the bran keeps the drum clean over multi-month periods, with no evidence of progressive biofilm formation.
Target Markets
We target regions with abundant cheap corn/wheat and strong fish/animal feed demand. Corn sugars are cheaper than molasses. Wheat works but requires endo-protease enzymes for gluten, offset somewhat by higher protein.
Country | Corn | Price | Wheat | Price |
---|---|---|---|---|
United States | 377 MMT/y | $157/MT | 54 MMT/y | $221/MT |
China | 295 MMT/y | $321/MT | 140 MMT/y | $285/MT |
Brazil | 132 MMT/y | $191/MT | 8 MMT/y | $231/MT |
Argentina | 50 MMT/y | $174/MT | 19 MMT/y | $232/MT |
Russia+Ukraine | 41 MMT/y | $175/MT | 105 MMT/y | $234/MT |
India | 43 MMT/y | $315/MT | 113 MMT/y | $293/MT |
Mexico | 25 MMT/y | $210/MT | 3 MMT/y | $262/MT |
Who are we?
Hamrick Engineering was founded in 2013 by Edward B. Hamrick.
Edward (Ed) Hamrick graduated with honors from the California Institute of Technology (CalTech) with a degree in Engineering and Applied Science. He worked for three years at NASA/JPL on the International Ultraviolet Explorer and Voyager projects and worked for ten years at Boeing as a Senior Systems Engineer and Engineering Manager. Subsequently, Ed worked for five years at Convex Computer Corporation as a Systems Engineer and Systems Engineering Manager. Ed has been a successful entrepreneur for the past 25 years.
Alex Ablaev, MBA, PhD is Sr. Worldwide Business Developer. Alex previously worked for Genencor's enzymatic hydrolysis division, and is the President of the Russian Biofuels Association as well as General Manager of NanoTaiga, a company in Russia using CelloFuel technologies in Russia.
Alan Pryce, CEng is Chief Engineer. Alan is an experienced professional mechanical engineer - Chartered Engineer (CEng) – Member of the Institute of Mechanical Engineers (IMechE) - with 10+ years’ experience in the mechanical design and project management of factory automation projects in UK and European factories. He has been a Senior Design Consultant and project manager for over 30 years working for Frazer-Nash Consultancy Ltd involved with many design and build contracts in the military, rail, manufacturing, and nuclear industries.
Maria Kharina, PhD, is Sr. Microbiology Scientist. Maria has a PhD in Biotechnology and is a researcher with 10+ years of experience. Maria was a Fulbright Scholar in the USA from 2016-2017.
Beverley Nash is Director of Marketing. Beverley has run Nash Marketing for over 30 years and has extensive experience in marketing planning and development for both new and established businesses. Beverley has worked for many global corporations in the technical marketplace and has been responsible for both the planning and management of many programs dealing with all aspects of company and product growth.
Dr. Ryan P. O'Connor (www.oconnor-company.com) provides intellectual property strategy consulting and patent prosecution. Dr. O'Connor holds a degree in Chemical Engineering from University of Notre Dame and a Ph.D. in Chemical Engineering from University of Minnesota. He has filed more than 1000 U.S. and PCT applications and is admitted to the Patent Bar, United States Patent & Trademark Office.
Hamrick Engineering Patent Portfolio
Contamination control when growing yeasts
U.S. Patent No. 12,297,423 status: Granted
International Patent App. No. PCT/US2023/083031 status: Published
CN118043470A (China) status: Published
RU2826104 (Russia) status: Granted
BR112024003499 (Brazil) status: Granted
Contamination control when growing yeasts - Continuation-In-Part
US Patent App. No. 19/202,827 status: Filed May 8, 2025
Methods for fermenting carbohydrate-rich crops
US9499839 (USA) status: Granted
RU2642296 (Russia) status: Granted
BR112016005352 (Brazil) status: Granted
CN107109440B (China) status: Granted
EP3140411 (European Union) status: Granted
AR106148A1 (Argentina) status: Granted
IN328228 (India) status: Granted
Notified of grant by Ukraine patent office
Method for fermenting stalks of the Poaceae family
US9631209 (USA) status: Granted
RU2650870 (Russia) status: Granted
EP3277825B1 (EU) status: Granted
MX363750B (Mexico) status: Granted
CN107849585B (China) status: Granted
BR112017008075 (Brazil) status: Granted
Methods and apparatus for separating ethanol from fermented biomass
US10087411 (USA) status: Granted
RU2685209 (Russia) status: Granted
EP3541489A1 (EU) status: Granted
MX371710 (Mexico) status: Granted
BR112018075838A2 (Brazil) status: Granted
IN332722 (India) status: Granted
CA3025016A1 (Canada) status: Granted
UA119630C2 (Ukraine) status: Granted
Methods and systems for producing sugars from carbohydrate-rich substrates
US9194012 (USA) status: Granted
RU9194012 (Russia) status: Granted
CA2884907 (Canada) status: Granted
CN105283468 (China) status: Granted
EP3004178 (European Union) status: Granted